Beyond standard features. Expand your Things5 platform
Build branded IoT applications that enhance Things5 capabilities.
Transform platform modules into tailored solutions that align with your product strategy and reflect your brand identity.
Our team specializes in developing
custom applications that
elevate your
user experiences
and
maximize the value
of your connected products.
How it works
CORE CAPABILITIES
Deliver the value of connected products straight to your users
Modular architecture
Each app is crafted from independent, reusable modules, selected to meet the specific needs of your product or processes. Create flexible, scalable solutions, seamlessly integrated with the Things5 ecosystem.
Mobile accessibility
We develop native mobile experiences that extend platform functionality, allowing users to monitor, control, and interact with devices anytime, anywhere.
Personalized product experiences
Offer unique experiences tailored to each user’s role, usage context, and machine type, enhancing usability and perceived value of your connected products.
How your IoT app born

CO-DESIGN
Let's design the digital experience together
We define goals, features, and user flows with you, identifying the most relevant modules for your users and connected machinesUpload unlimited content to Things5.

DEVELOPMENT & INTEGRATION
Build your app around your ecosystem
a
We develop the mobile app by integrating Things5 modules with existing systems (ERP, CRM, databases) to ensure perfect synchronization between physical products and digital experiences.

DEPLOYMENT & OPTIMIZATION
Grow the app with your users
a
Thanks to its modular architecture, your app evolves over time, with new features added to match your business growth and user needs.
a
Enhance your products' capabilities
Create your custom application
Every app is built from specific modules to address diverse business needs - from digitizing factory testing to simplifying end-user functionalities, with integrated support and commerce features.
User features
Service
Commerce
Factory testing
Digitalization and connectivity are strategic assets for competitiveness. For years, we’ve been helping manufacturers manage and leverage the growing wealth of data generated by their machines and devices.
Bluetooth pairing & cloud connection
PAIRING BLUETOOTH
Pain points
- Limited access to machine data remotely
- No standardized system for monitoring and collecting operational data
- Difficulties establishing reliable connections between machines and control devices
- Security concerns for remote access
Goals
Implement a standardized connectivity system to reduce machine setup and management time.
Solution
A fast, secure Bluetooth pairing process via mobile app offering:
- proximity-based monitoring & control, replacing physical displays
- simple QR-code pairing
- APP Gateway functionality, turning smartphones into data gateways for machines with limited connectivity.
CLOUD CONNECTION
Pain points
- Lack of remote machine data access
- No simplified network association procedures
- Limited real-time machine status monitoring
- Poor visibility of usage trends
Goals
Enable guided in-app procedures and simplify cloud data transmission.
Solution
A mobile app that:
- provides an intuitive interface for machine-to-cloud connection
- guides users step-by-step through the connection process.
OPTIONAL: SECURE MACHINE AUTHENTICATION
Creation of a fast and secure authentication system on the machine display via QR Code that allows the portability of settings and user programs/recipes from the cloud to the machine for a personalized user experience.
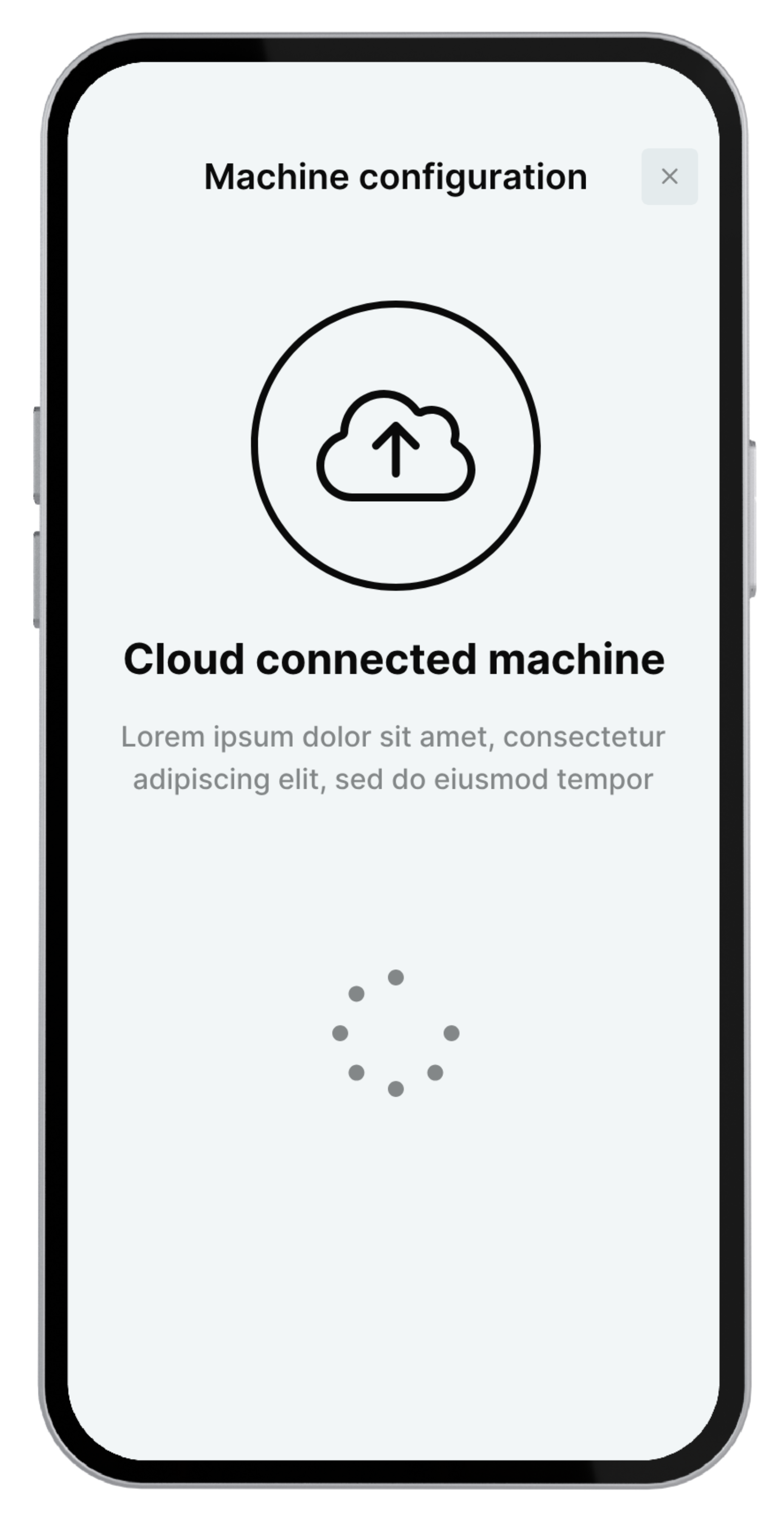
Machine setup process
Pain points
- Complex and time-consuming setup procedures
- Managing configuration for multiple devices
- Limited flexibility in customizing settings
Goals
Simplify Wi-Fi network setup and deliver a user-friendly connectivity solution.
Solution
Provide your customers with a mobile app that allows them to:
- easily connect the device to a Wi-Fi network
- select and configure their operational profile
- receive notifications about machine status and events
- configure machine features and parameters based on usage.
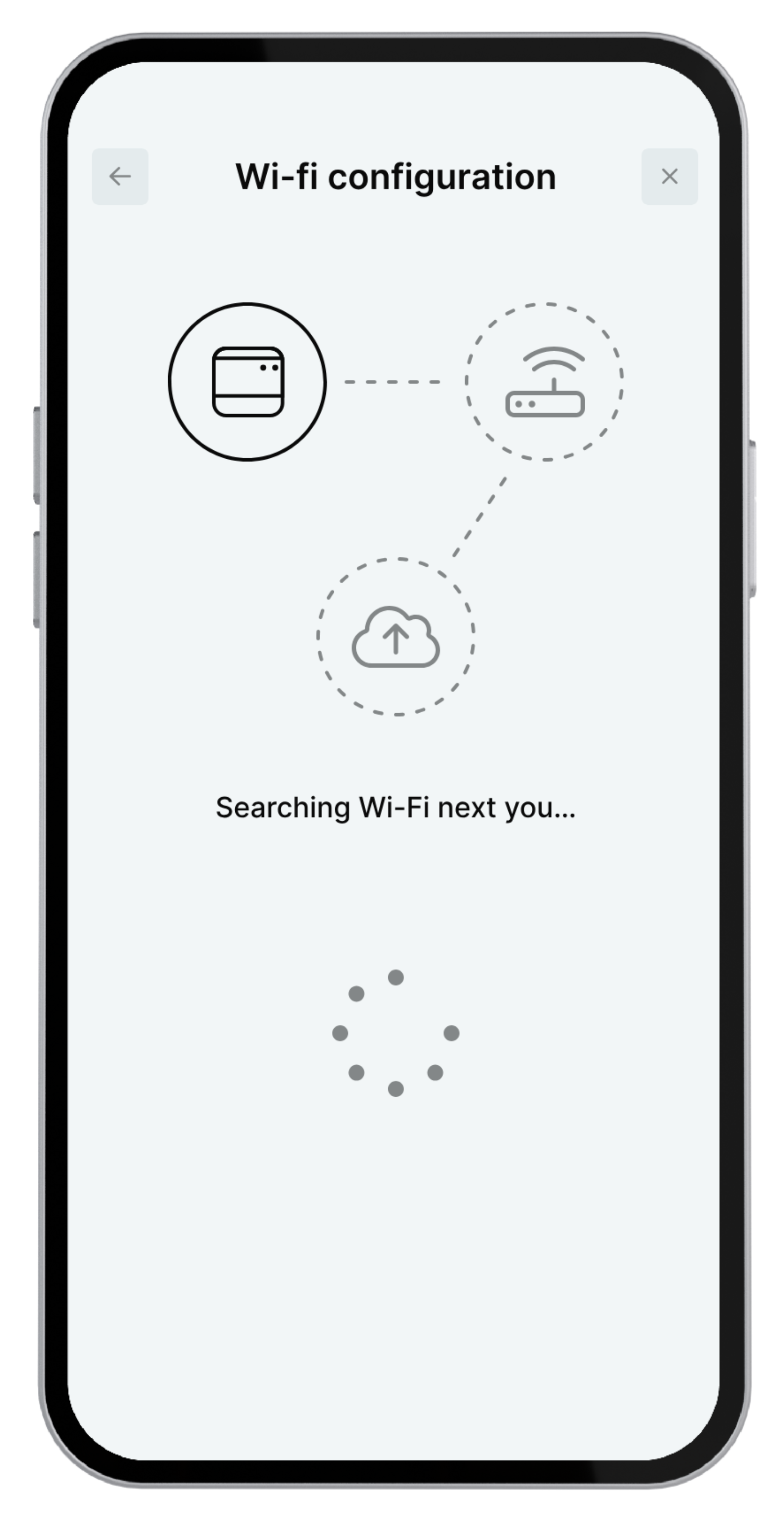
Machine control
Pain points
- Unintuitive interfaces limiting operational efficiency
- Lack of visibility into active programs/recipes
- Difficulty in transferring and standardizing machine settings
Goals
Enhance the user experience by extending machine controls beyond the physical display.
Solution
A mobile app that enables users to:
- start and stop machines remotely
- upload custom programs and recipes
- access real-time status and performance data
- define custom events based on specific triggers.
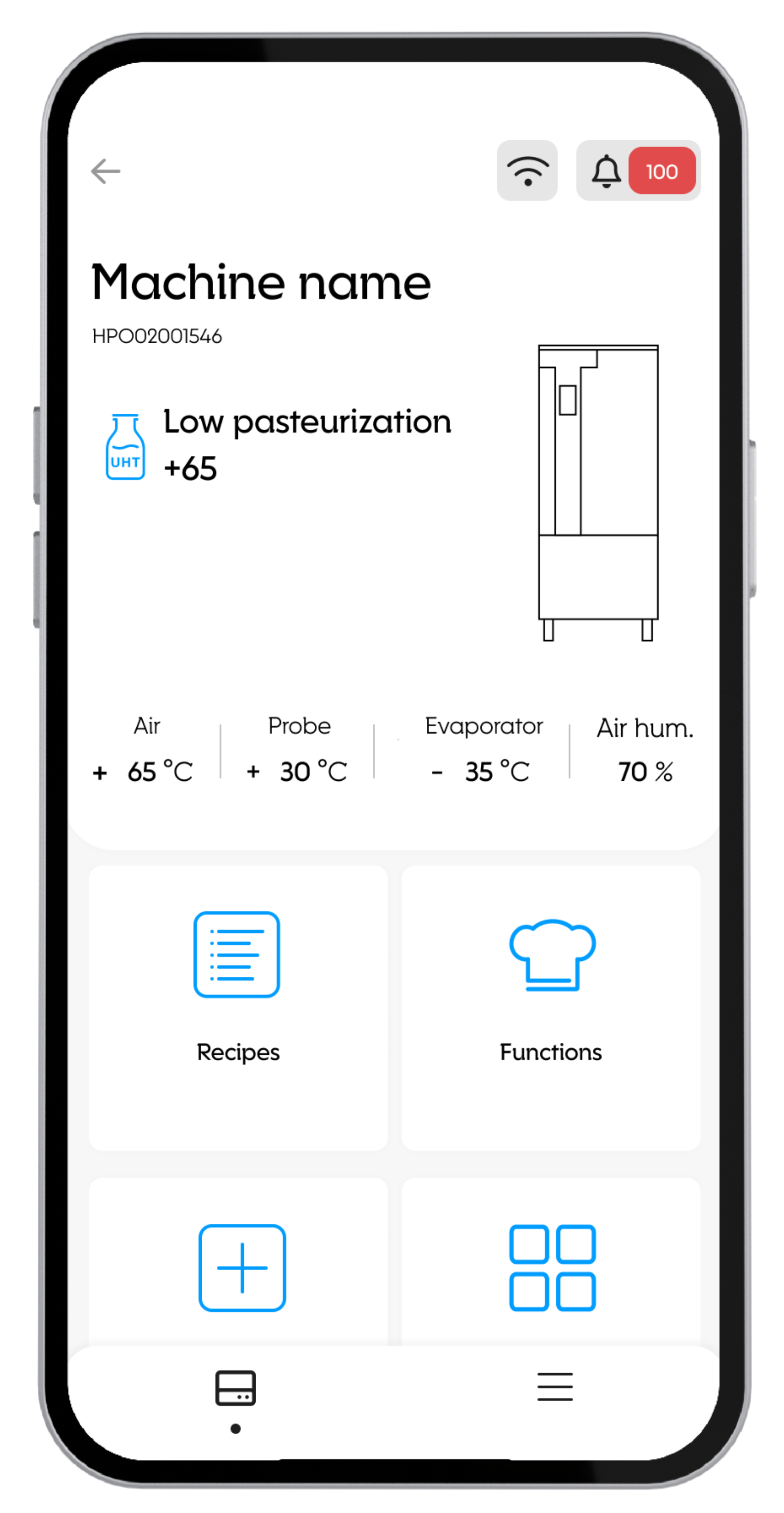
Real-time machine monitoring
Pain points
- No real-time visibility into machine performance
- Difficult access to machine alarms
- Inability to promptly detect inefficiencies or consumption anomalies.
Goals
Provide a detailed, time-filterable overview of machine status.
Solution
A mobile app offering:
- a comprehensive status dashboard
- detailed alarm views with resolution procedures
- time-range filters for data analysis
- in-depth exploration of specific data points.
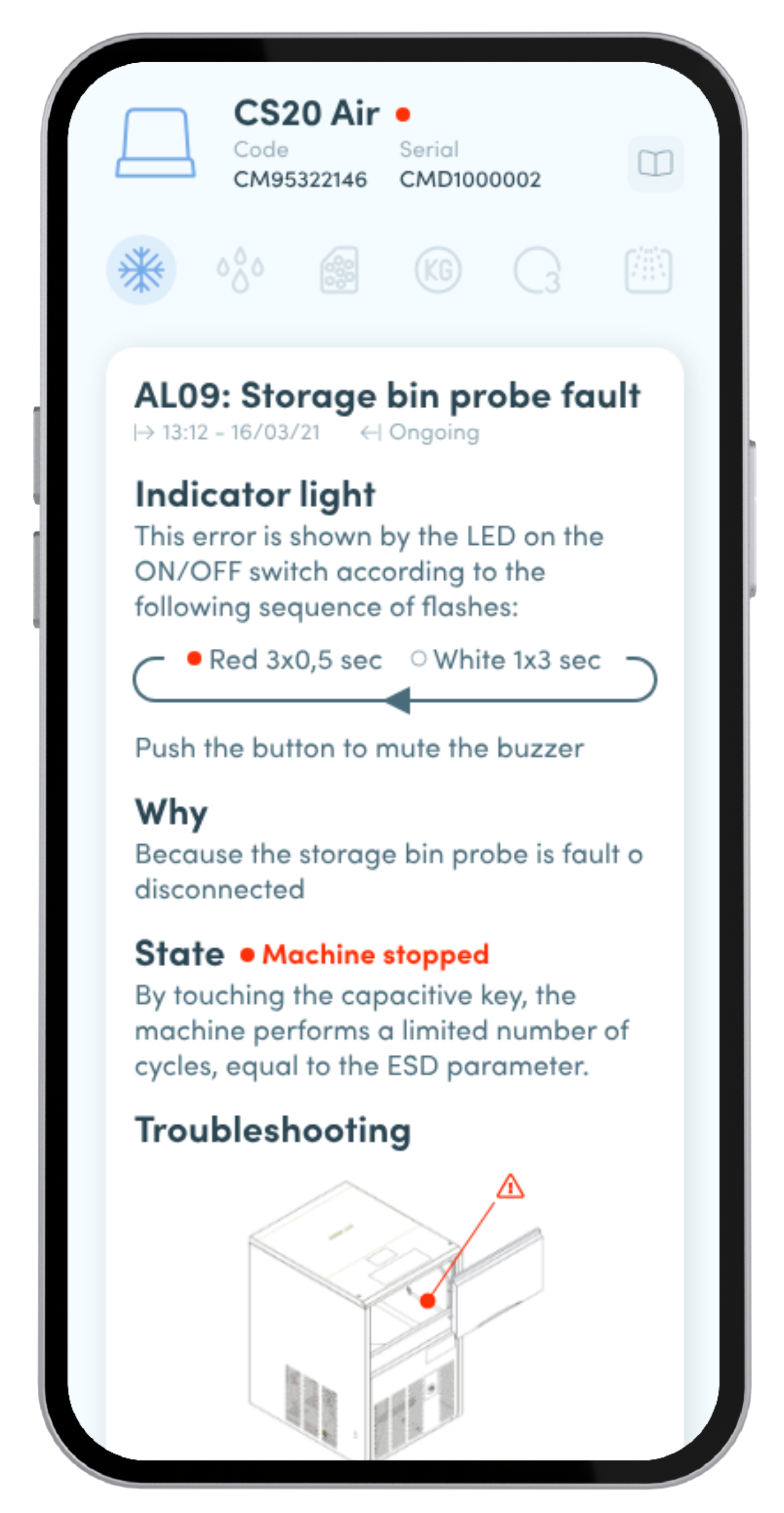
Parametrization
Pain points
- Time-consuming installation and configuration processes
- Difficulties managing and updating settings
- Lack of a centralized parameter archive
Goals
Streamline machine configuration and significantly reduce setup times.
Solution
A mobile app that lets users:
- safely view and edit all machine parameters
- load, overwrite, save, or import predefined configurations via USB
- save and consult past configurations and parameters.
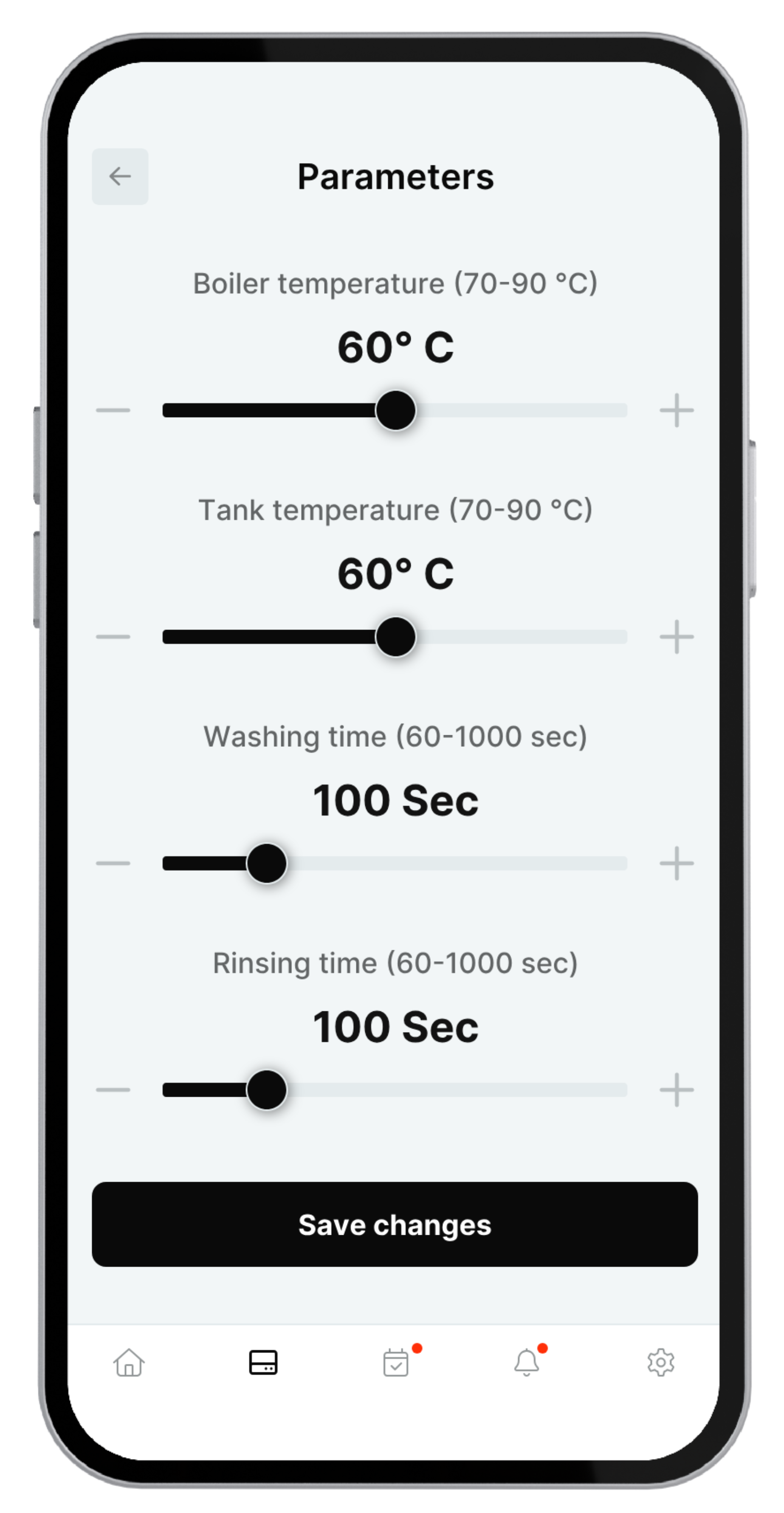
Program & recipe management
Problems
- No visibility on active programs/recipes
- Absence of a centralized system for creating and storing programs
- Complex deployment of programs on machines
- Limited access to archived recipes
Goals
Simplify remote program management and ensure seamless synchronization with the machine.
Solution
A mobile app that allows users to:
- manage machine programs and recipes in a centralized way
- synchronize settings automatically with the machine
- load, save, and replicate configurations effortlessly.
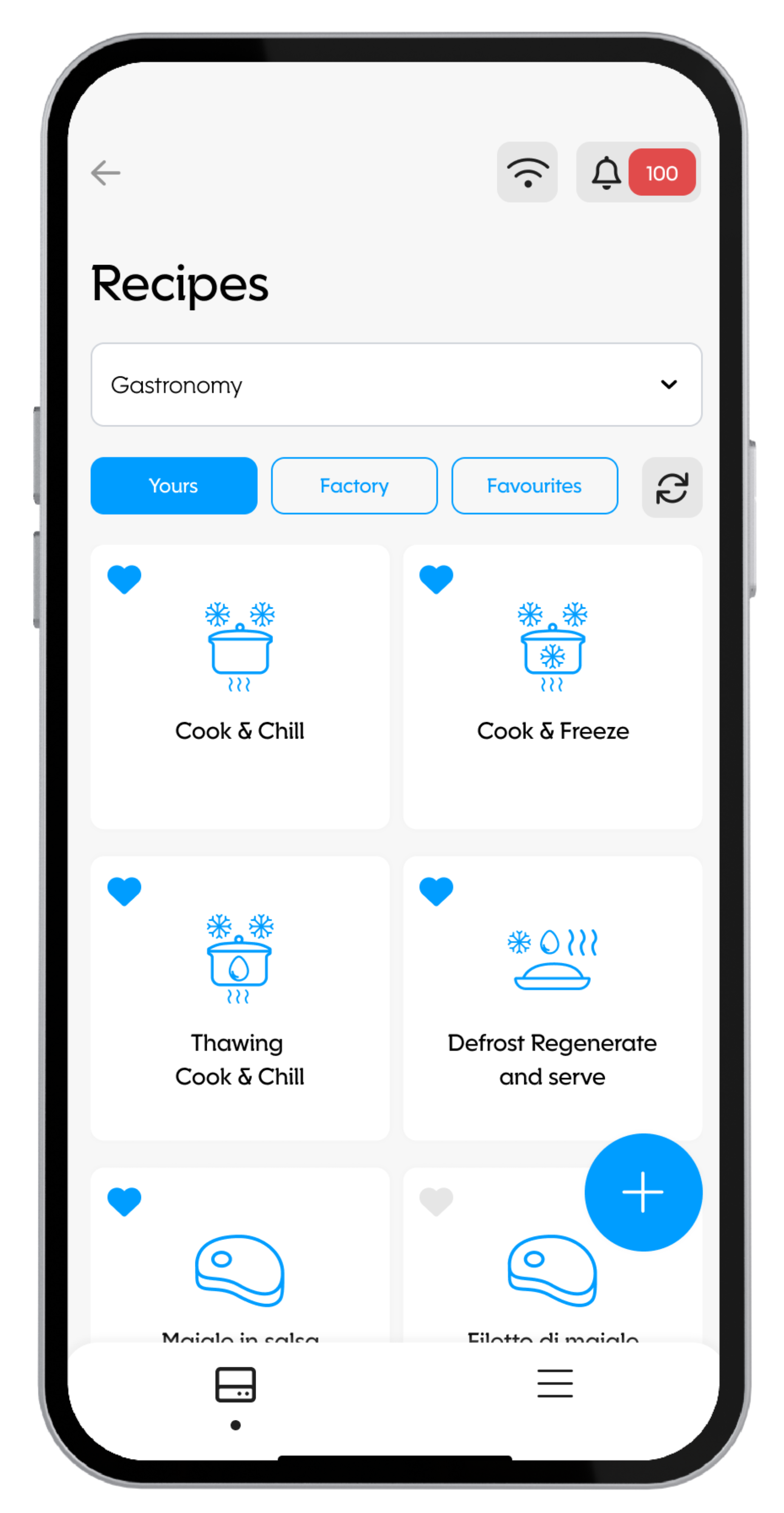
Analytics
Problems
- Lack of visibility into consumption and key machine variables
- Difficulty accessing historical data filtered by time periods
- Inability to quickly identify inefficiencies or anomalies
Goals
Deliver a clear and detailed view of machine performance with time-based filters.
Solution
A mobile app providing:
- summary statistics on energy consumption and production volumes
- interactive KPI dashboards and charts
- monthly recap notifications
- downloadable reports (e.g., HACCP compliance).
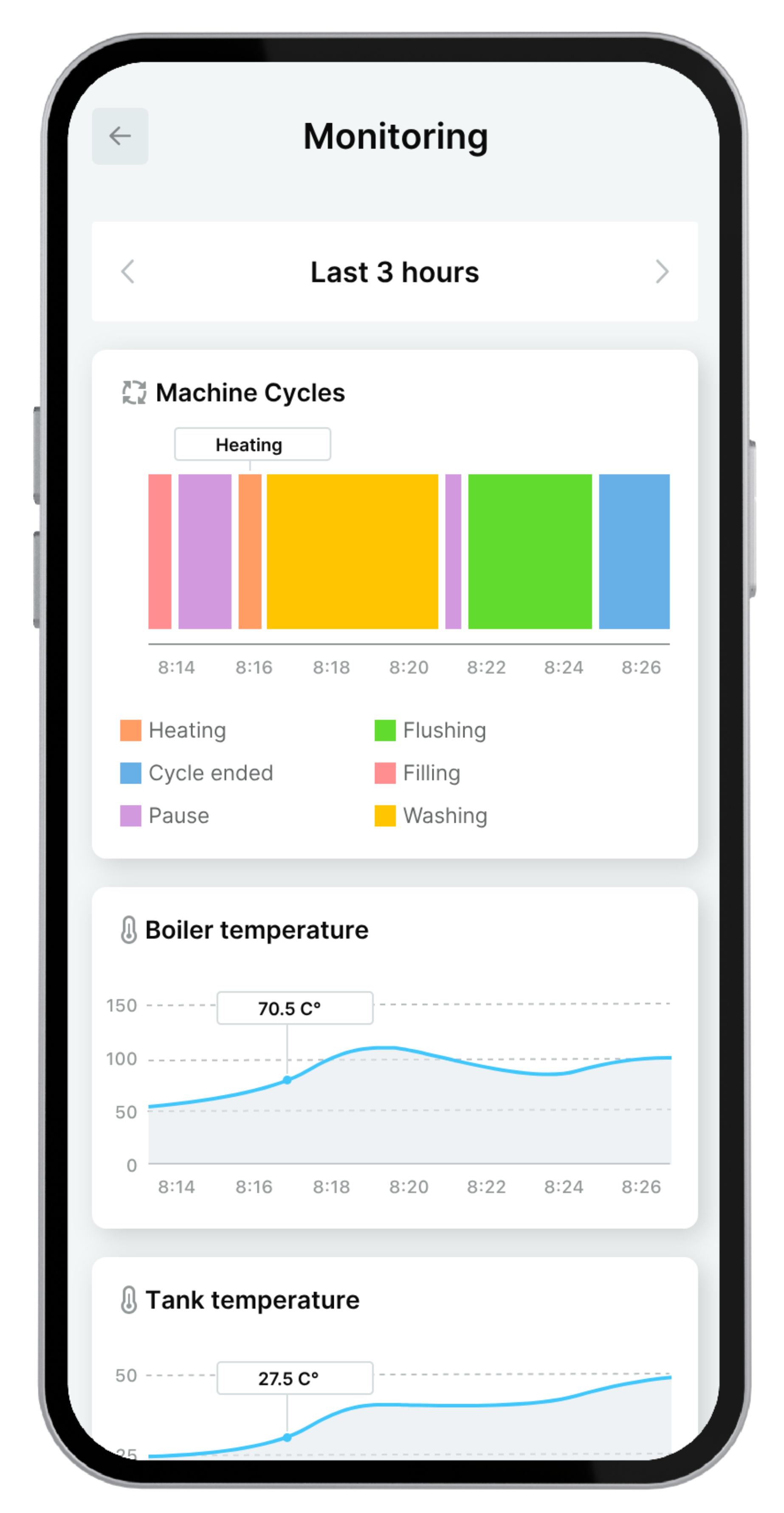
In technical support, speed and accuracy make all the difference. That’s why equipping technicians with intuitive, always-connected mobile tools has become essential.
The support modules turn smartphones and tablets into a true operational control center, enabling faster interventions, safer configurations, and more effective diagnostics - even remotely.
Extended parametrization
Pain points
- Limited access to advanced configuration options
- No centralized tool for remote technical management
- Lack of backup and sharable configurations
- High risk of manual errors due to non-standardized parameter handling
Goals
Centralize and digitize advanced machine configuration, eliminating legacy terminals and physical interventions.
Solution
An advanced parametrization module designed for service technicians, enabling them to:
- access all machine parameters in a secure interface
- quickly edit values using an integrated keypad with instant confirmation
- manage configurations in batch
- load parameter lists via USB for rapid replication across identical or replacement machines.
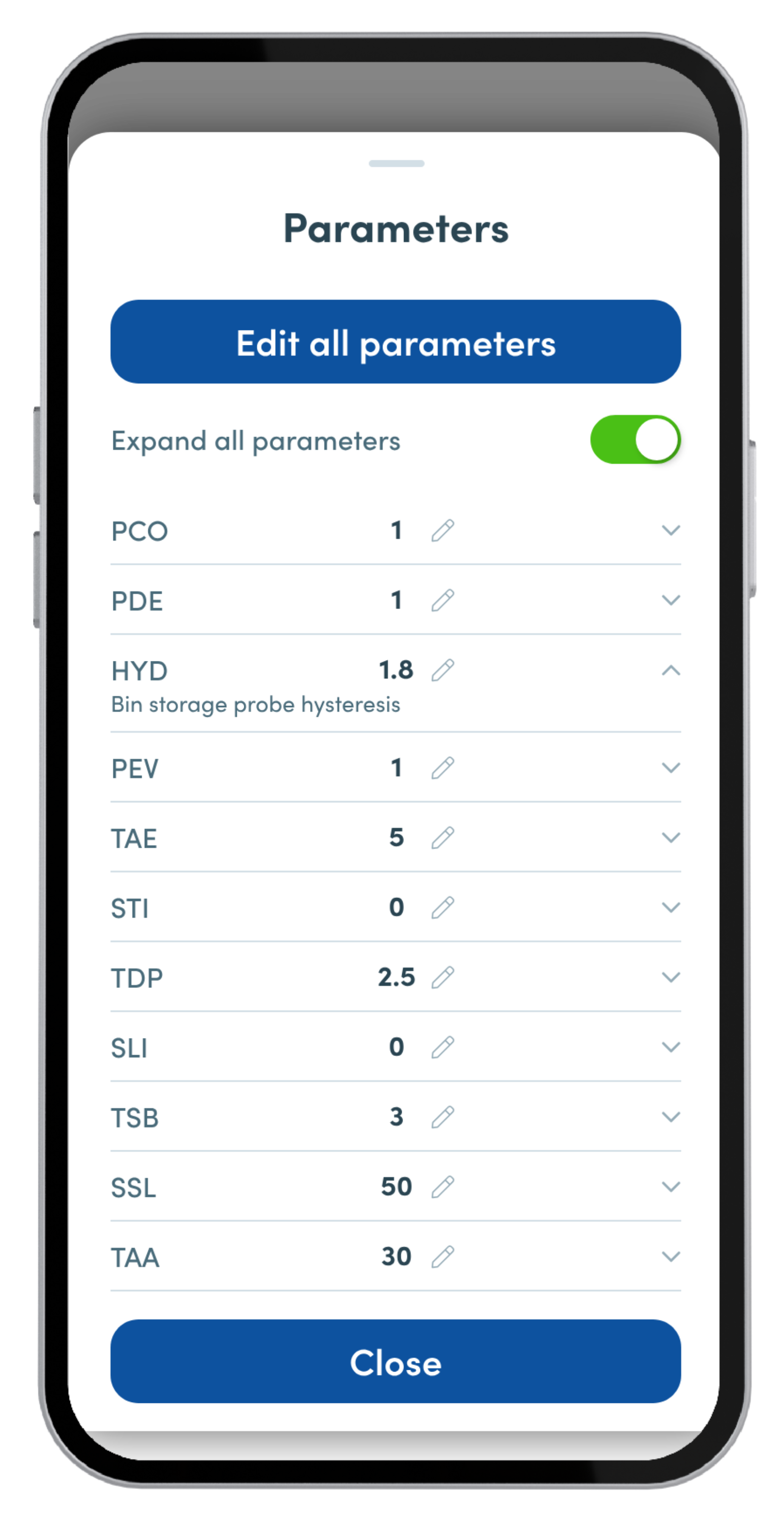
Machine synoptic view
Pain points
- Difficulties in understanding machine behavior
- Lack of visibility on critical variables over time
- Inefficient and time-consuming technical support requiring physical access to machines
Goals
Provide an intuitive, interactive overview of machine operations through synoptic visualization.
Solution
A dual-view interface within the mobile app offering:
Synoptic view
- Visual, stylized representation of functional flows
- Real-time data overlay on each component
- Immediate insight into operational cycles and anomalies.
Graphical view
- Interactive charts displaying critical variables
- Timeline visualization and multi-curve comparison for system validation
- Event tracking for deeper diagnostics.
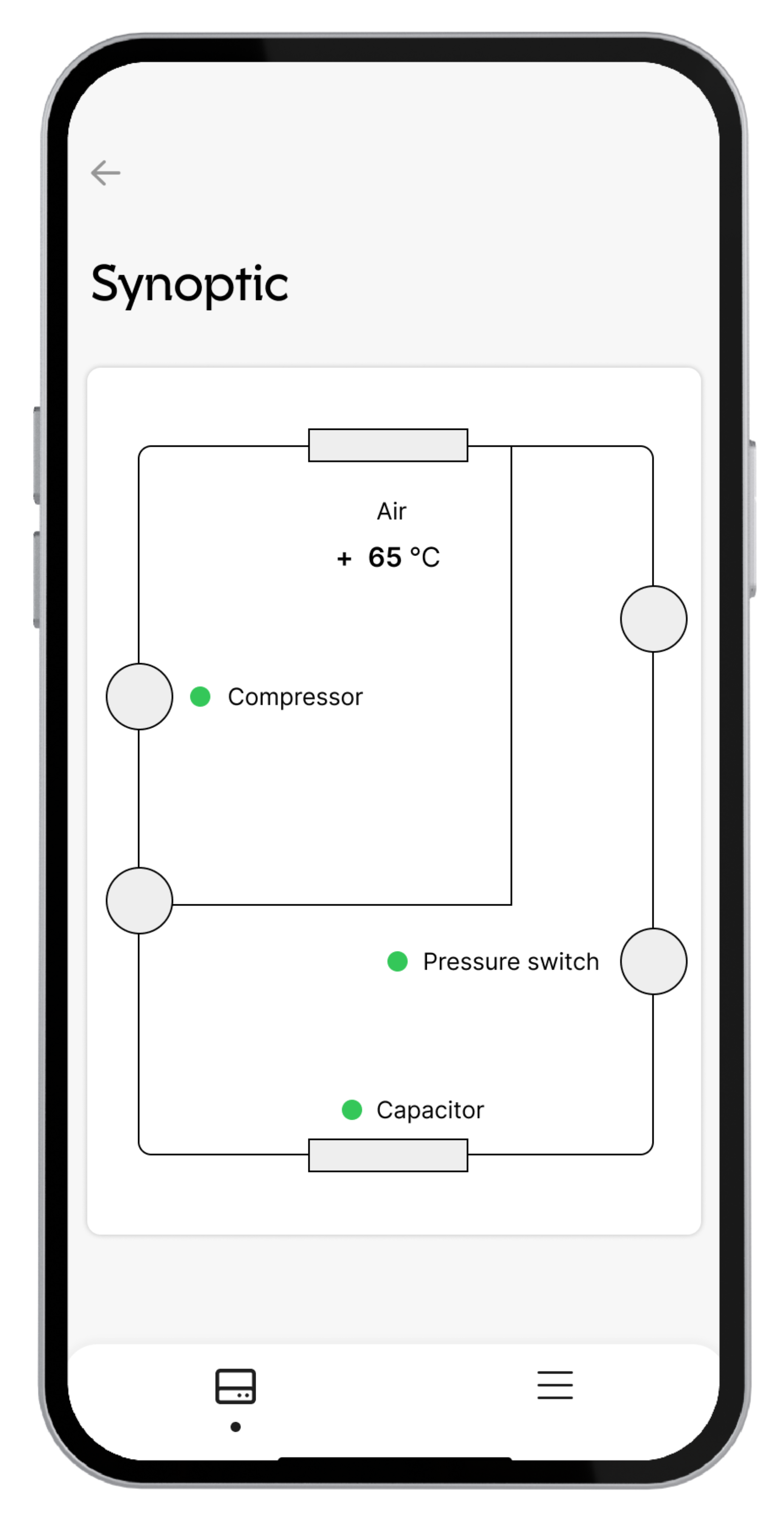
I/O data for specific components
Pain points
- Slow, unstructured technical diagnostics
- Dependence on external tools or physical inspections
- Lack of integrated testing capabilities
- No structured remote signal monitoring
Goals
Simplify access to critical data and reduce intervention times, even for less experienced technicians.
Solution
A real-time interface for monitoring and testing digital and analog signals, allowing technicians to:
- monitor INPUT signals live
- view a complete list of active components with real-time status
- run OUTPUT tests to verify proper functionality.
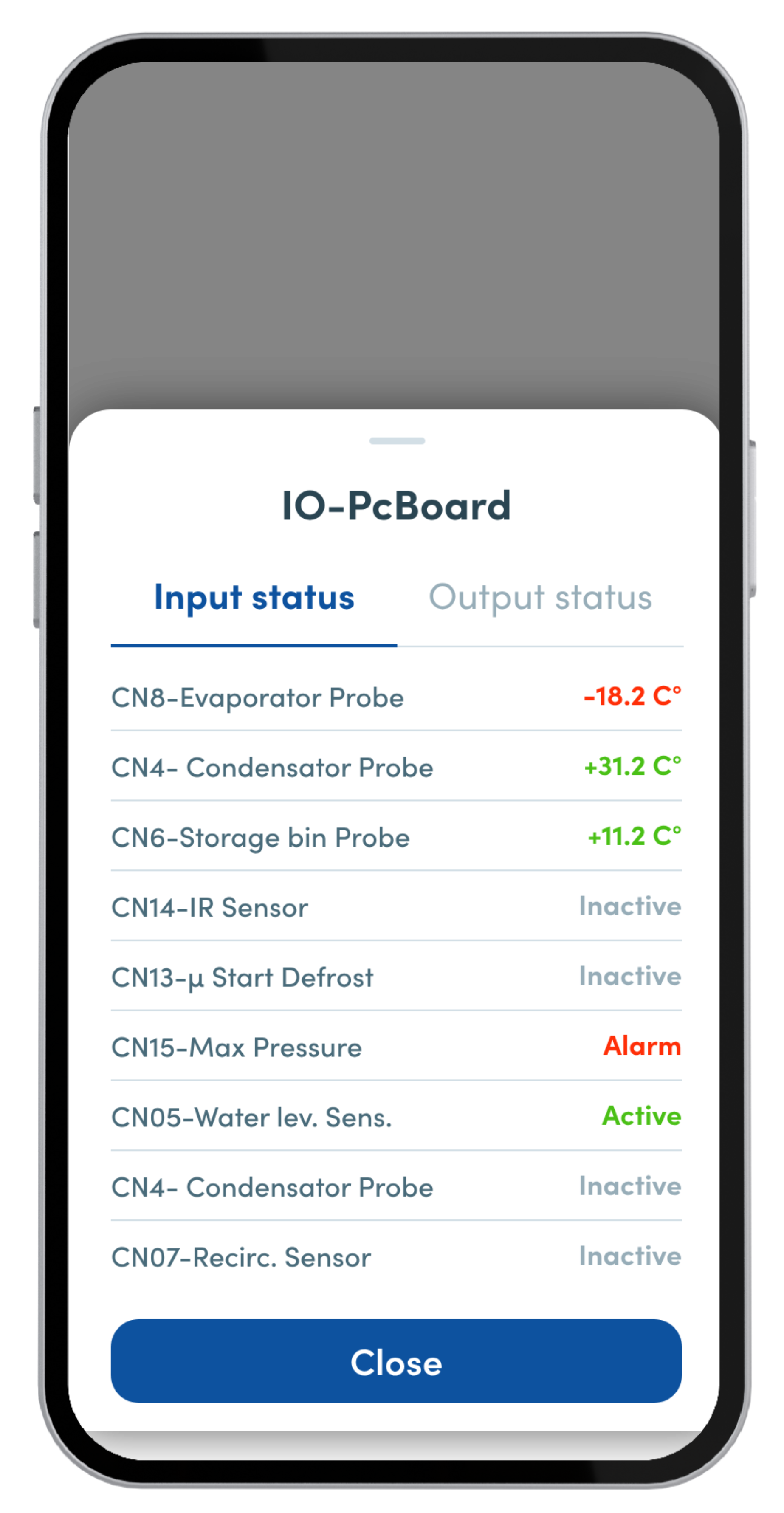
Troubleshooting management
Pain points
- Poor visibility on machine alarms
- Difficulty understanding error causes
- No integrated support for error resolution
- Lack of tracking for reports and resolutions
Goals
Deliver real-time, visual troubleshooting support to reduce reliance on external technical assistance.
Solution
An interactive alarm management module within the mobile app, providing:
- a comprehensive alarm list with status, code, description, and timestamp
- detailed alarm sheets with operational deactivation instructions
- bulk alarm reset functionality.
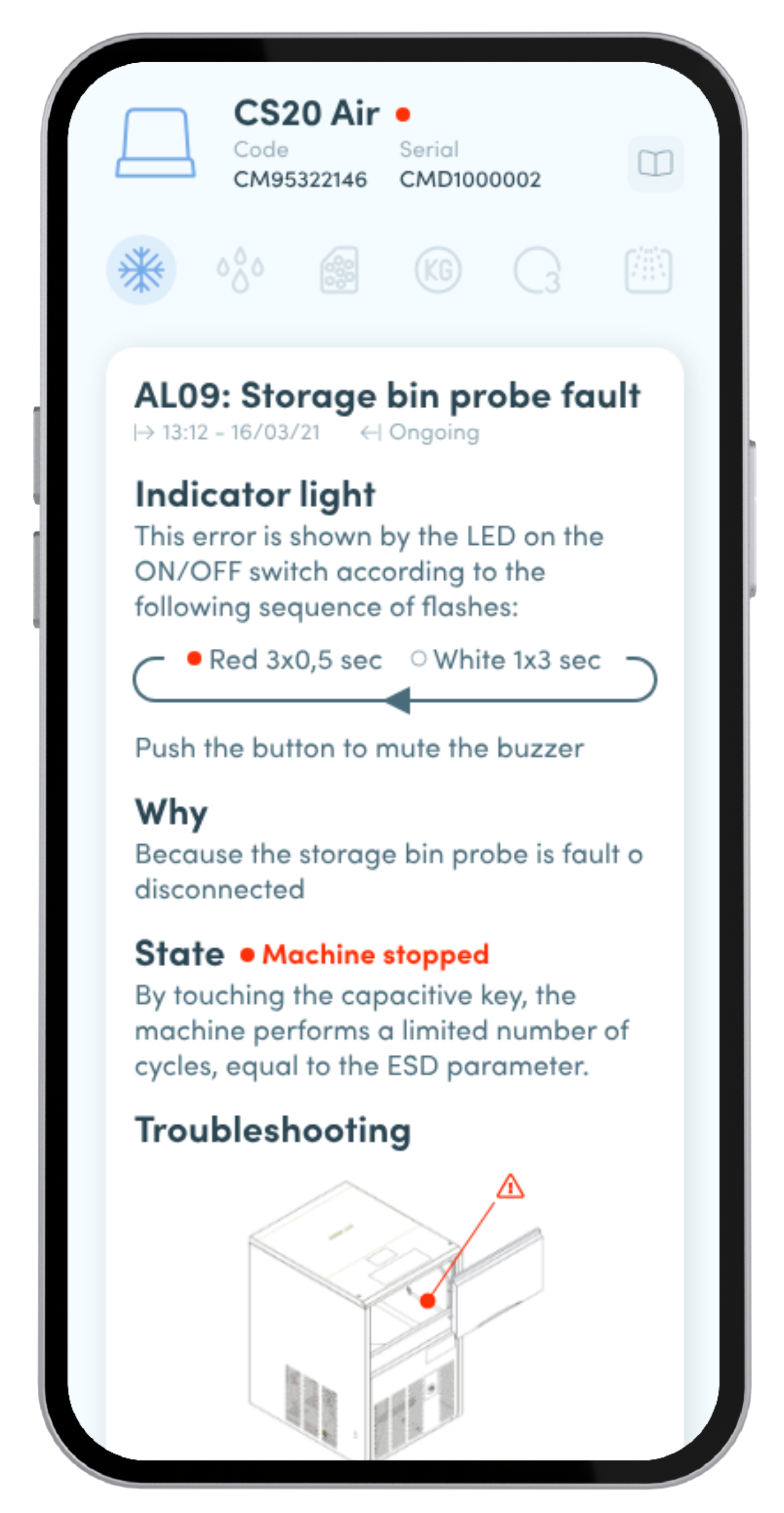
Ticket management
Pain points
- Fragmented, non-traceable support processes
- Long response times and poor prioritization
- No structured customer feedback post-intervention
- Difficulties managing attachments (photos, documents)
Goals
Digitalize the entire support workflow, giving customers full visibility on ticket status in real time.
Solution
A mobile module that ensures a smooth, fully trackable ticket management experience:
- simplified ticket creation by selecting machine model and describing the issue
- photo attachments for fault documentation
- ticket sorting by urgency and elapsed time
- feedback collection on post-sale service quality.
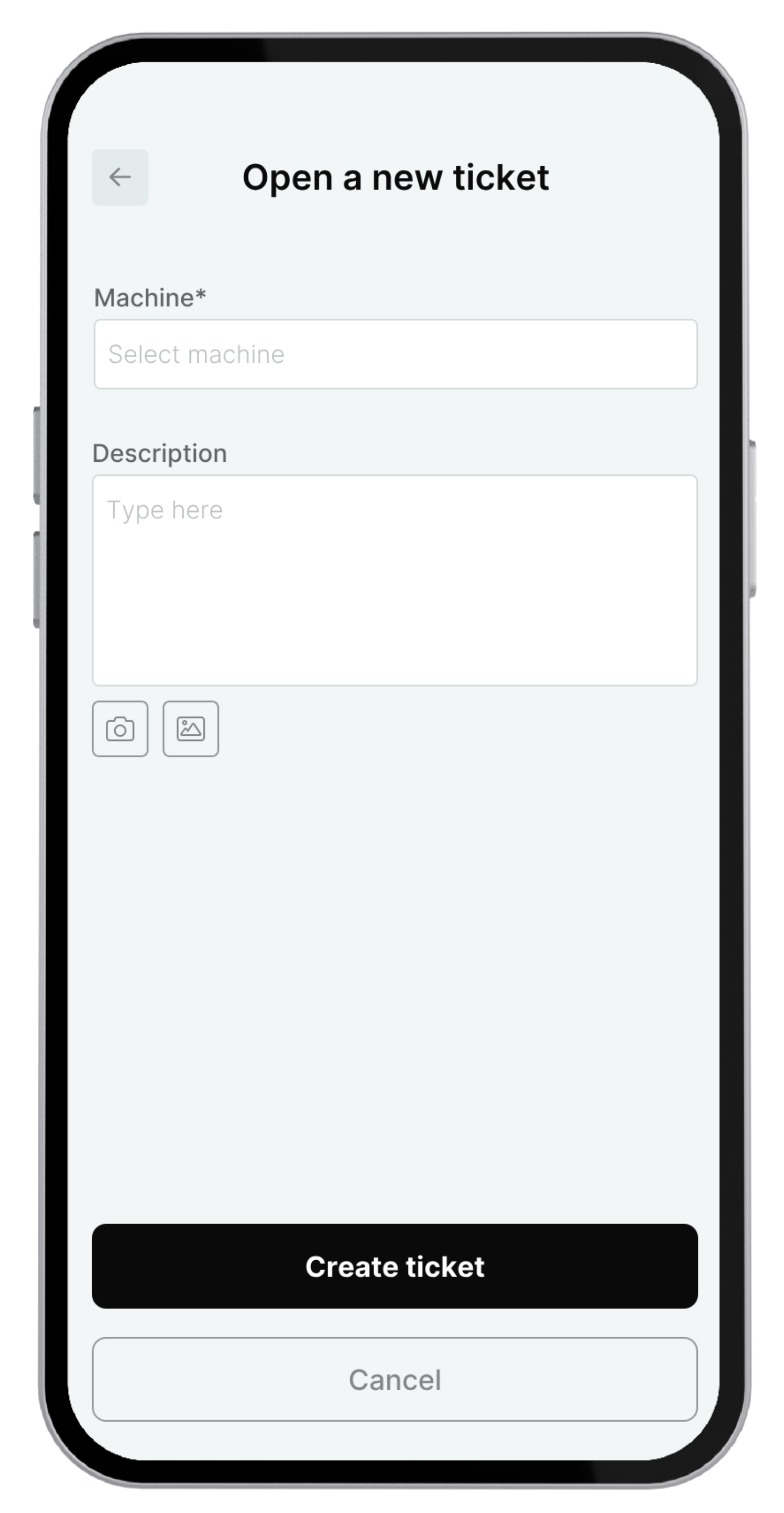
Your mobile app becomes a continuous touchpoint between your brand and your customers. Through dedicated modules, users can personalize their experience, unlock new product features, and keep their devices always at peak performance.
For manufacturers and brands, these modules are a real opportunity to create recurring value, boost customer loyalty, and build a digital service offering that enhances the physical product long after the initial purchase.
Service plan management
Pain points
- Customers unaware of warranty extensions or premium services
- Disconnection from end-users due to intermediaries
- Difficulty in maintaining long-term customer relationships post-sale
Goals
Extend customer engagement beyond the initial purchase by digitalizing service plan management.
Solution
A mobile module enabling customers to:
- view, activate, and manage support plans, warranty extensions, and premium services
- access detailed descriptions of available services
- complete payments or auto-renewals directly via the app
- receive renewal reminders and notifications.
Activation of new features
Pain points
- Advanced features underutilized due to poor promotion or activation complexity
- Customers unaware of product evolution over time
- Missed upselling opportunities post-sale
Goals
Adopt a “feature-as-a-service” model to gradually enhance product value and boost perceived innovation.
Solution
A dedicated module allowing users to:
- browse a catalog of available features for their device
- access detailed explanations and interactive demos
- activate new features in one click, with automatic compatibility checks and plan options (pay-per-use or subscription).
Consumables & spare parts purchase
Pain points
- Customers unsure which materials or spare parts are compatible
- Delayed replacements impacting product performance
- Disconnected purchase experience from product usage
Goals
Streamline the purchase of compatible materials directly from the app, fostering loyalty through a direct, automated channel.
Solution
An e-commerce module integrated with the machine profile, enabling users to:
- receive suggestions for compatible consumables and spare parts
- purchase items easily within the app
- get automated re-order notifications and personalized offers
- track orders and manage favorites.
Manufacturers need an efficient system to test and validate machines before shipment. However, operators are often still required to fill out paper forms and manually enter test data into IT systems, slowing down testing workflows and creating bottlenecks.
Machine testing & validation
Pain points
- Manual, error-prone testing and validation processes
- Delivery delays due to inefficient data handling
- Lack of real-time visibility into testing status
Goals
Digitalize the entire testing workflow for faster, more efficient, and fully traceable operations, with post-sale data availability.
Solution
Through an intuitive tablet/mobile interface, the module allows:
- access to simplified tools for test cycles and machine testing procedures
- automatic device registration in the cloud and data storage on Things5
- customizable dashboards for real-time reports and statistics
- easy machine connectivity via Wi-Fi/BLE interface.
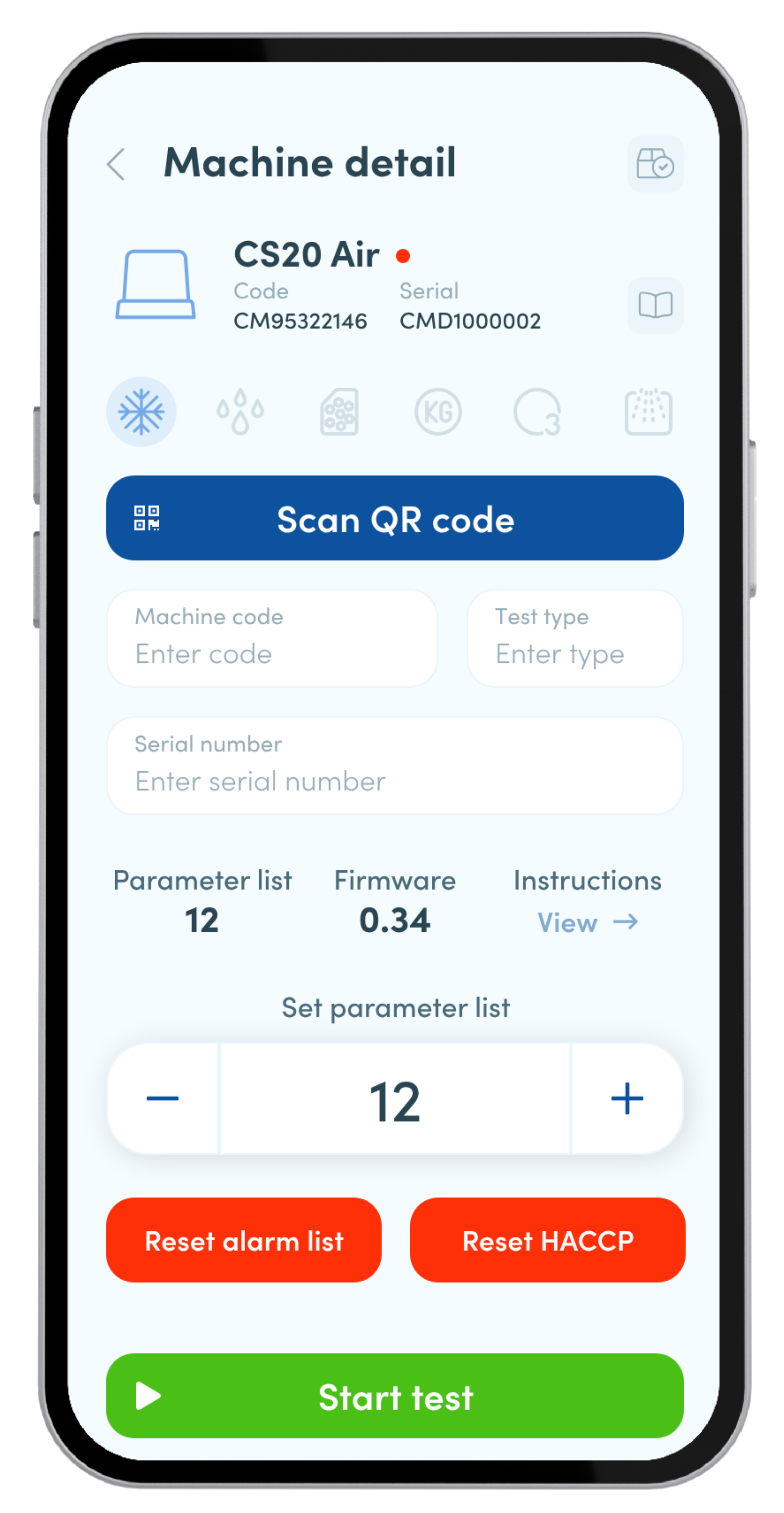
Bluetooth pairing
Pain points
- No access to machine data from remote locations
- Lack of standardized monitoring and data acquisition methods
- Unreliable machine-device connections
- Security concerns for remote access
Goals
Standardize connectivity and reduce machine setup and management times.
Solution
A fast, secure Bluetooth pairing procedure through a mobile app that provides:
- proximity-based control and monitoring, replacing physical displays
- instant pairing via QR code
- support for machines with limited connectivity capabilities through APP Gateway functionality that turns the phone into a gateway for sending data.
OPTIONAL: SECURE MACHINE AUTENTICATION
Creation of a fast and secure authentication system on the machine display via QR Code that allows the portability of settings on the machine for a personalized user experience.
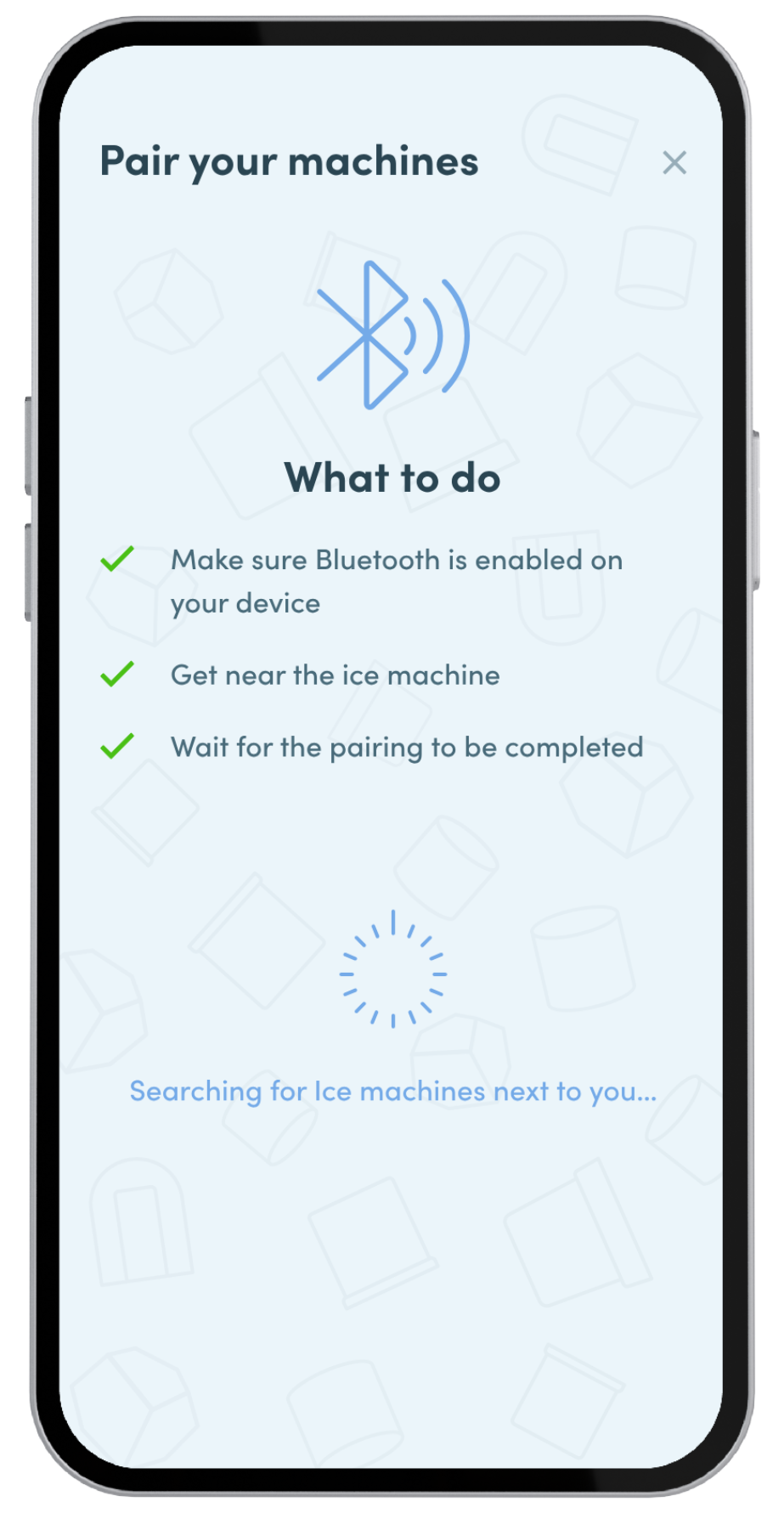